Baba Farid College of Engineering & Technology
Department of Mechanical Engineering
Department of Mechanical Engineering
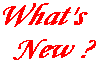
Friday, July 25, 2014
Thursday, July 24, 2014
Six-stroke engine
It is a type of internal combustion engine based on the four-stroke engine, but with additional complexity intended to make it more efficient and reduce emissions. Two types of six-stroke engine have been developed since the 1990s:
In the first approach, the engine captures the heat lost from the four-stroke Otto cycle
or Diesel cycle
and uses it to power an additional power and exhaust stroke of the piston in the same cylinder. Designs use either steam or air as the working fluid for the additional power stroke. The pistons in this type of six-stroke engine go up and down three times for each injection of fuel. There are two power strokes: one with fuel, the other with steam or air.
The second approach to the six-stroke engine uses a second opposed piston
in each cylinder that moves at half the cyclical rate of the main piston, thus giving six piston movements per cycle. Functionally, the second piston replaces the valve mechanism of a conventional engine but also increases thecompression ratio.
Laser Beam Machining (LBM)
It removes, melts, or thermally modifies a material by focusing a coherent beam of monochromatic light on the workpiece. The LBM process does not involve mass material removal, but does provide rapid material removal with an easily controlled, non-contact, nonwearing tool. The LBM process also places minimal demands on workpiece fixturing in cutting operations and performs a variety of other metal processing functions such as drilling, welding, marking, and heat treating. The effectiveness of LBM in a particular application depends on the pulsing and focusing of the beam and on the reflectivity, absorption coefficient, thermal conductivity, specific heat, and heat of vaporization of the workpiece. The greatest use of lasers is in metal cutting, primarily two-axis profiling of sheet goods that might otherwise have been blanked out by punch press or fabricated by hand after laborious layout of the pattern. Currently, most metal cutting falls within 9.5 mm (0.375 in.) and thinner, although CO 2 lasers are now competitive with plasma arc cutting for metal thicknesses of 13 mm (0.500 in.) and greater. The principal factor in the use of laser metal cutting is manufacturing methodology. Laser cutting is ideal for batch processes, just-in-time, or low-to-medium volume production. Most laser-cutting work is performed on generic or multipurpose material handling systems, as opposed to dedicated automation controlled systems. Generally, there is a clear-cut reason for using one type of laser over another.
Carbon dioxide lasers are capable of delivering much higher average power than Nd:YAG lasers. As such, CO2 lasers can cut faster and produce deeper weld penetration than Nd:YAG lasers. Pulsed Nd:YAG lasers develop a high pulse energy that allows percussion drilling and the cutting of metals at angles and thicknesses not possible with CO2 lasers. There are some applications—spot welding and hole cutting, for example—where either laser type can provide acceptable results at comparable speeds. Capabilities and operating ranges for CO2 and Nd:YAG lasers are shown in Tables and . Laser welding is becoming increasingly used in both low-volume specialty production and high-volume assembly operations. Laser welding operations are typically more dependent on lengthy process development than are cutting applications. Often parts are specifically designed to be laser welded. Laser welding generally requires more precise part fit-up than arc welding processes. While most laser welding is autogenous, that is, without added filler metal, it is becoming apparent that the addition of filler metal to bridge gaps or to act as a buffer when joining metals has great potential.
Water Jet Cutting
A water jet cutter, also known as a water jet or waterjet, is an industrial tool capable of cutting a wide variety of materials using a very high-pressure jet of water, or a mixture of water and an abrasive substance. The term abrasivejet refers specifically to the use of a mixture of water and abrasive to cut hard materials such as metal or granite, while the terms pure waterjet and water-only cutting refer to waterjet cutting without the use of added abrasives, often used for softer materials such as wood or rubber.
Waterjet cutting is often used during fabrication of machine parts. It is the preferred method when the materials being cut are sensitive to the high temperatures generated by other methods. Waterjet cutting is used in various industries including mining and aerospace for cutting, shaping, and reaming...
Stress-strain diagram for ductile materials
Ductile materials, which includes structural steel, as well as many alloys of other metals, are characterized by their ability to yield at normal temperatures.
Low carbon steel generally exhibits a very linear stress–strain relationship up to a well defined yield point . The linear portion of the curve is the elastic region and the slope is the modulus of elasticity or Young's Modulus. After the yield point, the curve typically decreases slightly because of dislocations escaping from Cottrell atmospheres. As deformation continues, the stress increases on account of strain hardening until it reaches the ultimate strength. Until this point, the cross-sectional area decreases uniformly because of Poisson contractions. The actual rupture point is in the same vertical line as the visual rupture point.
However, beyond this point a neck forms where the local cross-sectional area decreases more quickly than the rest of the sample resulting in an increase in the true stress, On an engineering stress–strain curve this is seen as a decrease in the apparent stress. However if the curve is plotted in terms of true stress and true strain the stress will continue to rise until failure. Eventually the neck becomes unstable and the specimen ruptures (fractures).
Less ductile materials such as aluminum and medium to high carbon steels do not have a well-defined yield point.There are generally two types of yield points,upper and lower yield point. For these materials the yield strength is typically determined by the "offset yield method", by which a line is drawn parallel to the linear elastic portion of the curve and intersecting the abscissa at some arbitrary value (generally from 0.1% to 0.2%). The intersection of this line and the stress–strain curve is reported as the yield point. The elastic region is the portion of the curve where the material will return to its original shape if the load is removed. The plastic region is the portion where some permanent deformation will occur, even if the load is removed. Failure point is when the object ruptures.
Low carbon steel generally exhibits a very linear stress–strain relationship up to a well defined yield point . The linear portion of the curve is the elastic region and the slope is the modulus of elasticity or Young's Modulus. After the yield point, the curve typically decreases slightly because of dislocations escaping from Cottrell atmospheres. As deformation continues, the stress increases on account of strain hardening until it reaches the ultimate strength. Until this point, the cross-sectional area decreases uniformly because of Poisson contractions. The actual rupture point is in the same vertical line as the visual rupture point.
However, beyond this point a neck forms where the local cross-sectional area decreases more quickly than the rest of the sample resulting in an increase in the true stress, On an engineering stress–strain curve this is seen as a decrease in the apparent stress. However if the curve is plotted in terms of true stress and true strain the stress will continue to rise until failure. Eventually the neck becomes unstable and the specimen ruptures (fractures).
Less ductile materials such as aluminum and medium to high carbon steels do not have a well-defined yield point.There are generally two types of yield points,upper and lower yield point. For these materials the yield strength is typically determined by the "offset yield method", by which a line is drawn parallel to the linear elastic portion of the curve and intersecting the abscissa at some arbitrary value (generally from 0.1% to 0.2%). The intersection of this line and the stress–strain curve is reported as the yield point. The elastic region is the portion of the curve where the material will return to its original shape if the load is removed. The plastic region is the portion where some permanent deformation will occur, even if the load is removed. Failure point is when the object ruptures.
Tuesday, July 22, 2014
Subscribe to:
Posts (Atom)